5-minute read - by Christine Middleton, July 17, 2023
At ASML, we don’t innovate in isolation. Our supply chain is crucial to our success and we’ve always relied on our suppliers to manufacture many of the components that go into our lithography systems. In fact, about 80% of the bill of materials of our machines is manufactured by our suppliers. That means we can focus on architecting and integrating the most advanced chip equipment in the world, pushing technology to new limits.
Our rapid growth over the past few years and the ways in which the COVID-19 pandemic stretched global supply chains to their limits have highlighted just how important it is to work closely with suppliers around the world. That’s why we prioritize nurturing and growing those relationships. By partnering closely with and supporting our suppliers, we’re ensuring that they’re prepared to work with us for years to come – and to weather the changes that the chip industry is known for, including periods of rapid growth and business-cycle fluctuations.
Here are 6 ways that we’re preparing our supply chain for the future.
1. Enabling a sustainable supply chain
ASML aims to take a leading role in ESG (environmental, social and governance) sustainability in the semiconductor industry. We have several ambitious targets in place for the next decade and beyond. One key goal is working toward net-zero greenhouse gas emissions in our supply chain by 2030. To achieve this, our Sourcing & Procurement team’s core objective is active collaboration with our suppliers to increase ESG sustainability maturity.
Previously, our ESG sustainability efforts centered on supplier engagement and sharing CO2 emissions data. Moving forward, suppliers will be asked to look beyond basic emissions data and share their sustainability roadmaps and goals with us. Our sourcing teams will be trained on ESG topics in the second half of 2023 and will work closely with our suppliers to help develop their ESG sustainability strategies and capabilities.
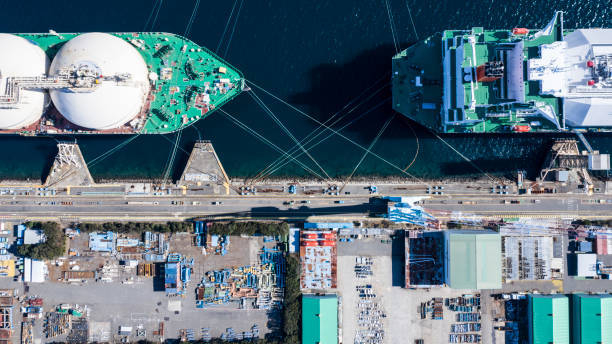
2. Collaborating much more closely to truly understand each other
To support better process alignment with our suppliers, we introduced our Supplier Collaboration Program in 2022. The program places experienced colleagues at our suppliers’ sites, typically for 4–6 months, to gain insights into their ways of working and collaborate on technology and production roadmaps.
The information we share through our Supplier Collaboration Program is helping us understand and, when necessary, address business dependencies. By spending time with our suppliers, our people can develop a better understanding of their businesses and identify who has the capacity to grow with us without becoming overly dependent. This holistic approach also feeds into the strategy that we build with them moving forward.
3. Growing our supply chain to match the needs of the industry
In addition to helping our existing suppliers grow with us, we’re also working to expand our supplier network.
Onboarding a new supplier isn’t something we take lightly. A new supplier needs to learn our company culture, way of working, and requirements on quality and delivery. That’s why we’ve introduced transfer teams that manage these transitions and further develop the cross-sectoral onboarding process. Because the teams know what to expect, they can take steps to make the integration process easier.
In addition, the chip industry is an intense pressure cooker. ASML often does in parallel what other companies may do sequentially, so we can save time and get technology to our customers as quickly as possible. For example, we go through many versions of a part design in quick succession before settling on a final design. And even after we settle on a part design, the quantity needed remains relatively small because we only manufacture several hundred lithography machines every year.
To help new suppliers get up to speed as quickly as possible, we’ve added information about how we work to new supplier management briefings. The information is also incorporated into onboarding and training materials so everyone knows what to expect.
4. Mitigating production risks and bottlenecks
In chip manufacturing, time is money, so we’re always on the lookout for potential risks to our production planning. Because our suppliers play such an important role in the timely delivery of parts and modules, it’s no wonder that we closely monitor and optimize our supply chain.
One such area is scarce materials – for example, the rare earth metals that go into the magnets in our machines. They come from only a few locations worldwide, so the availability of a particular metal can vary based on economic and geopolitical conditions.
For example, in the past we used a particular mixture of rare earth metals to make our magnets. So to mitigate ASML’s exposure to this risk, our engineers identified a second combination that can do the same job. Now we have two options that we can use depending on availability and market developments.
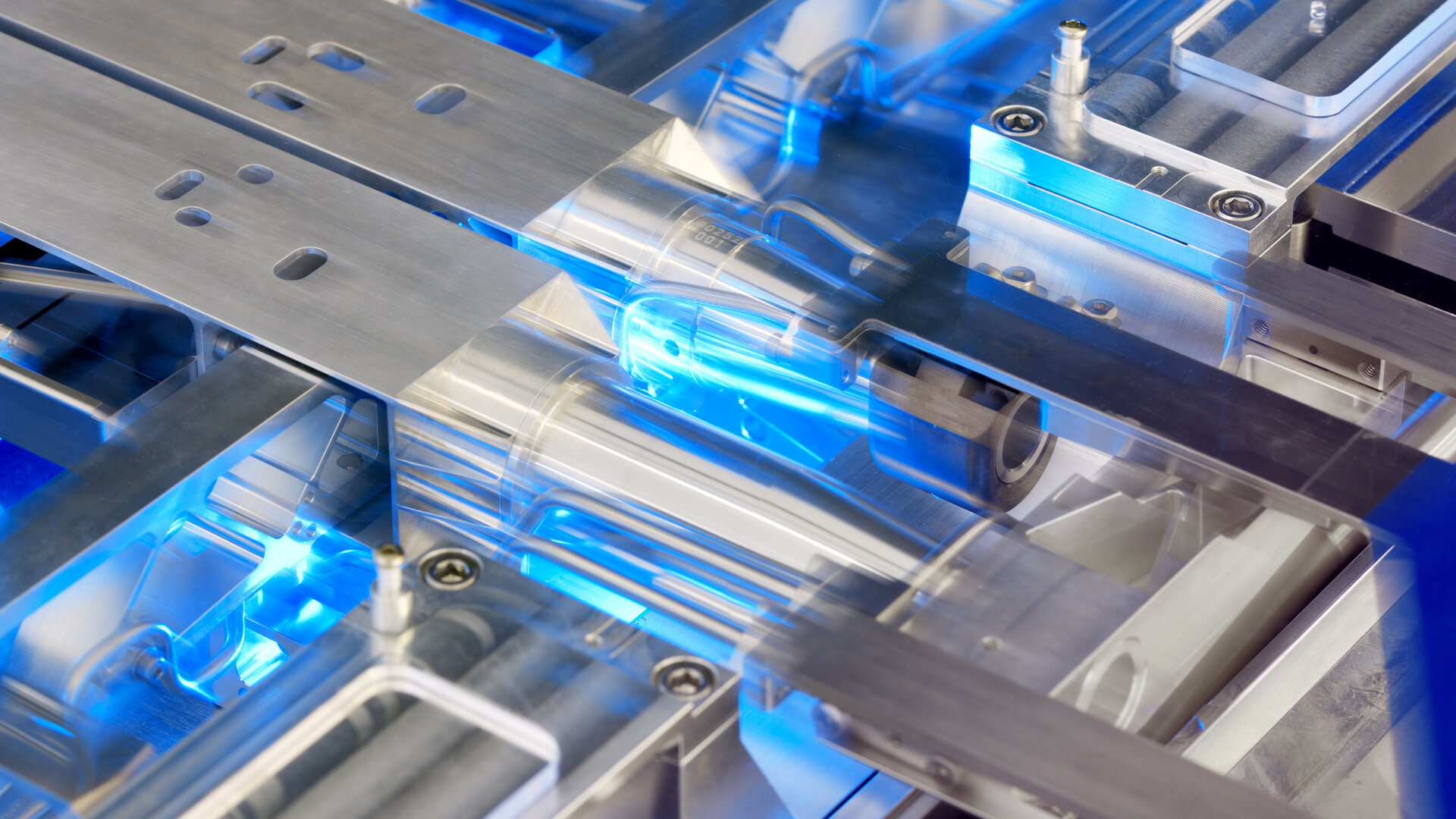
5. Building local repair centers with local suppliers
Our customers are located around the world, while our main campus is located in the Netherlands. So it can be costly – both in time and resources – to ship parts to and from our Veldhoven campus for repair. That’s why we’re building local repair centers in our customers’ regions. We currently have centers in the Netherlands, the US, Taiwan, South Korea and China. And we plan to eventually have at least one center in every customer region.
By building local repair centers, we create local supply ecosystems. The centers work with local material suppliers and specialized repair partners to provide our customers with the services they need in a more timely and cost-effective way. And, because the parts don’t have to travel as far, local repairs produce fewer greenhouse gas emissions. By 2025, we aim for 10% of all parts in the field that need service to be repaired locally.
6. Attracting talent to our full ecosystem
Every new ASML employee at our global headquarters in Veldhoven leads to 2.5 additional people in our supply chain. ASML is poised to double in size in the Netherlands – from 20,000 to 40,000 people – by 2030 and that means an additional 50,000 people working for suppliers throughout our network.
And because we know how challenging it is to find engineering talent, we want to help our suppliers grow by sharing our talent pool. Sometimes we have an easier time attracting applicants than our suppliers do because ASML is a more recognizable name. But the skills we’re looking for are often quite similar. In those cases, we seek approval from the applicants to share their information with our suppliers, who are also looking for qualified candidates.
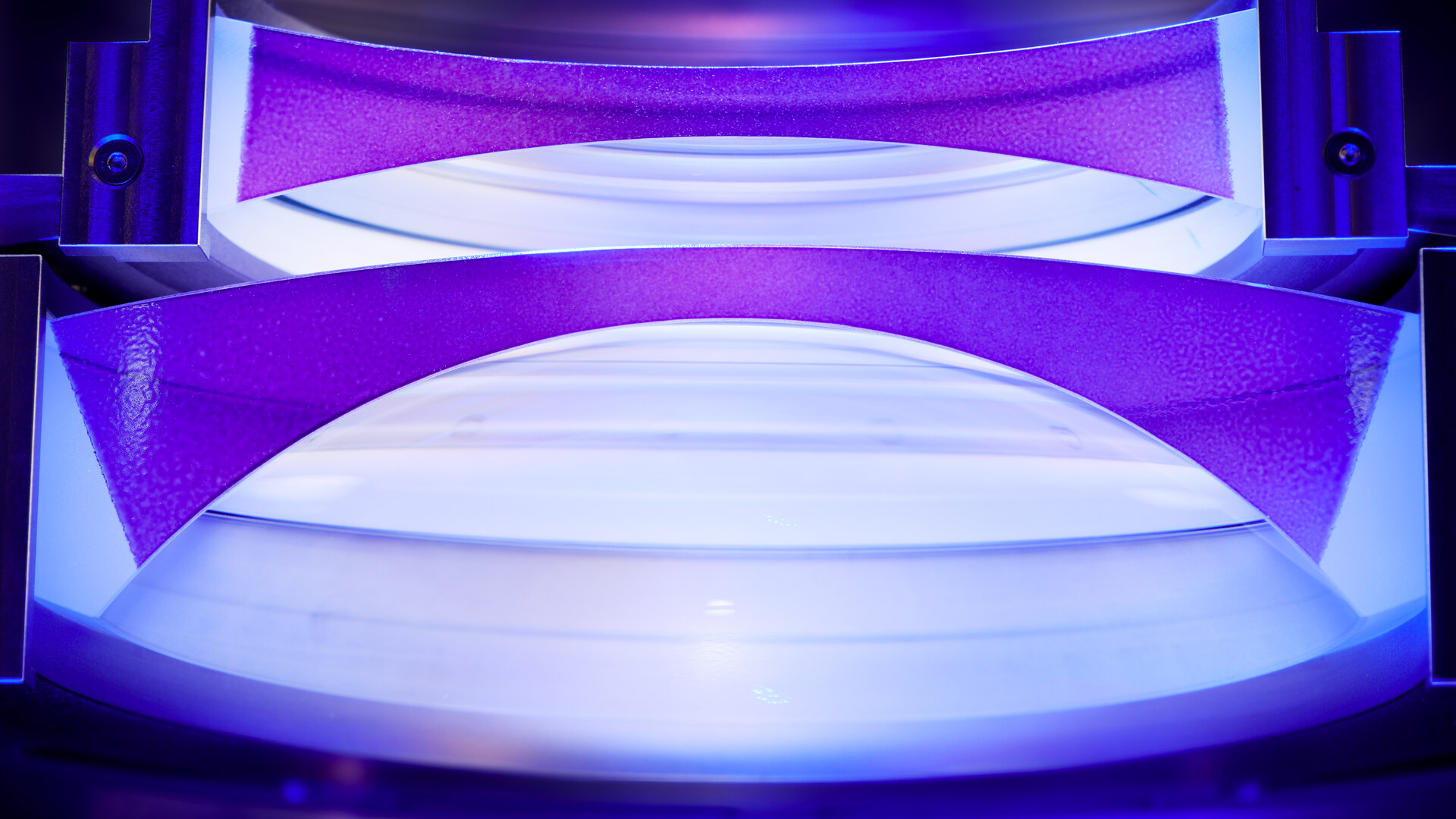